自分たちで自分たちの職場をより良くする現場KAIZENシリーズ。
今回は多種多様な材料を取り扱っている包装加工課で保管作業を効率化した事例になります。
生産現場で使用する多種多様な材料の保管管理
包装加工課ではシートの切り抜き加工を行うマルチカッターを用い、多種多様な発泡材シートの加工を日々行っています。一度使用して半端になった発泡シートでも出荷完了まで保管する必要があるため、パレットに積み重ね保管を行っていました。多種多様な端材が出てくるため、保管管理に苦慮していました。
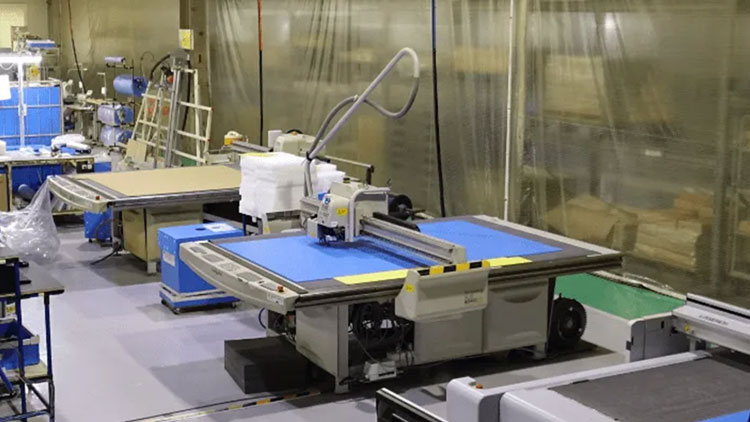
安易なパレットへの積み重ねが保管効率と作業性を悪化させる
何種類もの材料が上へ上へと積み重ねられていくことで、乱雑で取り出しにくくなる悪循環が起きていました。多種多様な発泡シートを使用するので端材が出るたびに積み重ねられていきます。下の方に積まれた発泡シートが必要になった場合、上に積み重ねたシートを移し替える作業のムダと、マルチカッターまで材料を持っていく移動の手間が発生していました。
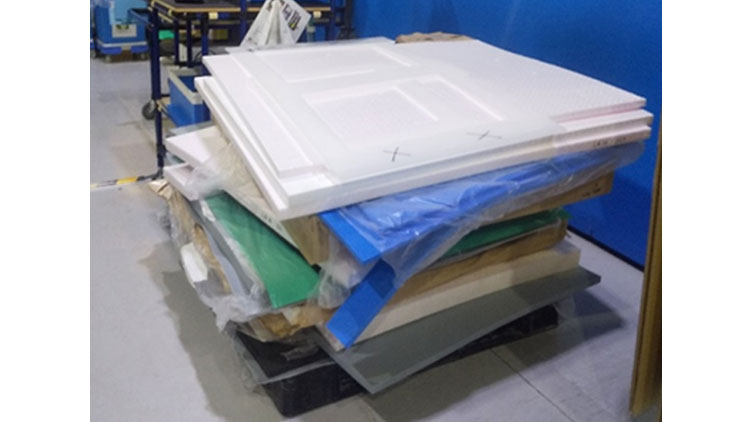
生産現場で知識を持ちよりKAIZENにつなげる
パイプ台車の製造を行っているパイプラインの担当者に、保管兼運搬用の台車が作れないか図案化したものを持ちよって相談することにしました。
寸法やパイプ部材の位置の調整、底板の材質といった台車の仕様をワイガヤ(※1)して決め、技術部員に詳細図面の作成に協力してもらいました。生産現場でのワイガヤでそれぞれの知識を持ちよることで、作業者にとって理想的な運搬台車が仕上がりました。
※1:ワイガヤ:「ワイワイガヤガヤ」、複数人が集まり気軽に議論をかわすこと
大幅に作業効率をUPするパイプ台車での立てかけ保管
パレットに積み重ねていた時よりも見た目が良くなり、シートが取り出しやすく、整理整頓も楽になりました。パイプ台車ごと機械のわきに端材を持ち込めるため、マルチカッターからシート置き場までの往復距離が10歩から4歩に削減。1回あたり6歩×1日に約4回の削減となりました。パレットでの横置き保管からパイプ台車での立てかけ保管に変えることで、保管効率と移動時の作業効率UPの効果が得られました。
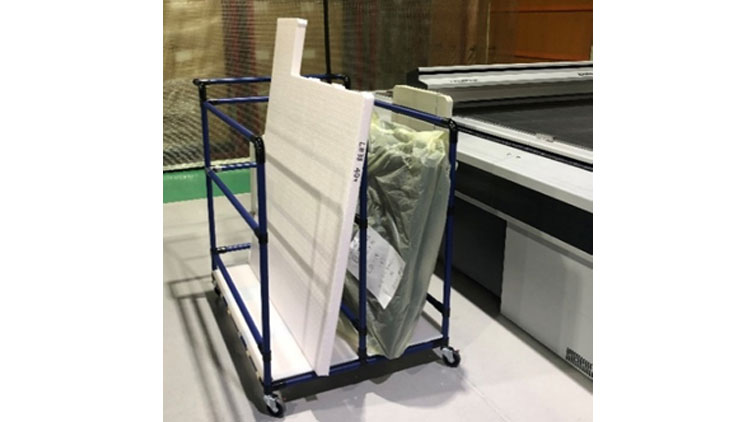